Common Applications of Chemical Defoamer Across Different Sectors
The Importance of Using a Chemical Defoamer in Different Applications
The application of chemical defoamers is a necessary consideration across several sectors, consisting of food handling, wastewater therapy, and drugs. These representatives play a crucial duty in mitigating foam development, which can impede effectiveness and compromise product quality. The advantages of making use of defoamers expand past simple appearances; they are critical for accomplishing compliance with industry standards and enhancing operational processes. Nevertheless, the systems whereby defoamers function and their specific applications raise further questions about their total influence and performance in these diverse contexts. What understandings can be uncovered concerning their use?
Comprehending Foam Formation
Foam development is a complicated physical phenomenon that takes place when gas bubbles are caught within a liquid matrix, resulting in the production of a steady framework. This process can be affected by different aspects, consisting of the thickness of the fluid, the surface stress at the gas-liquid interface, and the presence of surfactants. Surfactants lower the surface area tension, promoting bubble production and stablizing, which frequently causes the development of foam in several industrial processes.
Foams are typically run into in applications such as food production, wastewater therapy, and chemical manufacturing. In these contexts, foam can work as an insulator, conflict with blending procedures, or hinder the efficiency of devices. The stability of foam is established by the equilibrium in between the pressures acting to stabilize the bubbles and those that advertise their collapse.
Comprehending the auto mechanics of foam formation is essential for effectively managing its presence in different systems. By comprehending the underlying concepts, markets can devise techniques to mitigate undesirable frothing, consequently improving operational performance and item top quality. This foundational understanding serves as a precursor to checking out the energy of chemical defoamers, which particularly attend to foam-related difficulties in various applications.
Benefits of Chemical Defoamers
Chemical defoamers supply significant benefits across various sectors by efficiently minimizing and regulating foam development. By decreasing foam, chemical defoamers assist preserve optimum manufacturing rates and lower downtime linked with foam administration.
Furthermore, chemical defoamers add to improved product quality. Frothing often leads to inconsistencies in formulations, which can adversely influence the end product. By managing foam degrees, defoamers make sure harmony, therefore enhancing the overall top quality of the result.
Cost-effectiveness is an additional significant benefit (Chemical Defoamer). By decreasing the quantity of basic materials needed for production and lowering waste, chemical defoamers can cause considerable financial savings. They typically allow for reduced power consumption, as procedures can run a lot more smoothly and call for less treatment.
Applications in Food Processing
In the food handling market, efficient administration of foam is vital to ensure both item quality and functional effectiveness. Foam can hinder numerous processes, from mixing and blending to packaging, leading to minimized returns and prospective contamination. Chemical defoamers play a critical duty in minimizing these concerns by rapidly damaging down foam, allowing for smoother procedures and enhanced product consistency.
In applications such as milk processing, defoamers stop excess foam development during the manufacturing of yogurt, milk, and cheese, which can disrupt equipment and affect the appearance of the final item. Likewise, in brewing and fermentation processes, foam control is vital to keep the honesty of the drink and guarantee ideal fermentation prices.
In addition, chemical defoamers are made use of in food dressings, emulsions, and sauces to improve the stability and appearance of the last items. By decreasing foam during manufacturing, manufacturers can achieve better mixing and dispersion of active ingredients, causing remarkable top quality. Overall, the unification of chemical defoamers in food processing is essential for preserving performance, quality, and security in food production.
Duty in Wastewater Treatment
Effective foam management is equally important in wastewater treatment procedures, where excessive foam can hinder procedures and make complex the therapy of effluents. In several wastewater therapy centers, foam can develop as a result of biological activity, surfactants, or various other natural products existing in the influent. why not find out more This foam can cause a series of operational challenges, including reduced therapy performance, raised upkeep needs, and possible regulative conformity concerns.
Chemical defoamers play an essential function in alleviating these difficulties. By minimizing the surface tension of the fluid, defoamers promote the collapse of foam frameworks, thus helping with smoother operation of tools such as aeration tanks and clarifiers. Their timely application assists maintain ideal hydraulic conditions, boosting the overall effectiveness of solids separation procedures.
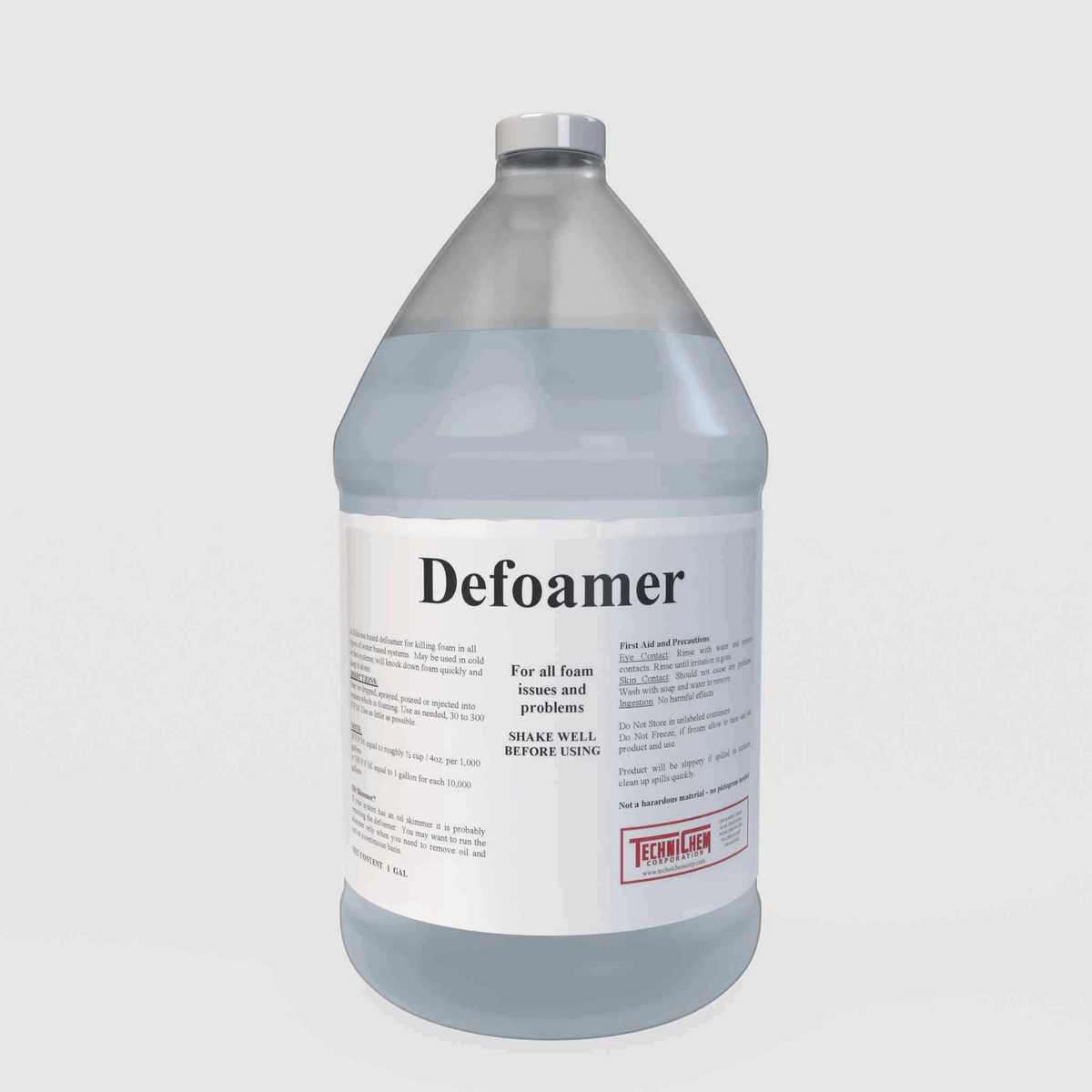
Influence on Drug Manufacturing
Foam control is vital in pharmaceutical manufacturing, where the presence of excessive foam can disrupt manufacturing procedures and concession product high quality (Chemical Defoamer). The formation of foam during various phases, such as blending, mixing, and fermentation, can result in inefficient mixing, poor warmth transfer, and also devices damages. These concerns not just result in operational hold-ups yet can additionally cause substantial financial losses and influence compliance with rigorous governing requirements
Chemical defoamers are particularly formulated to reduce these challenges. By effectively lowering foam development, they improve procedure performance and maintain the stability of the end product. In particular, defoamers make sure constant dose types, improve the security of suspensions and solutions, and simplify cleaning processes by protecting against foam accumulation in equipment.
Additionally, making use of defoamers can maximize the return of active pharmaceutical active ingredients (APIs) by promoting much better removal and purification processes. As pharmaceutical business strive to boost item high quality while lessening production expenses, the role of chemical defoamers ends up being increasingly crucial - Chemical Defoamer. Their incorporation into making procedures not just supports conformity with Good Production Practices (GMP) but additionally fosters technology and competition in a quickly developing sector
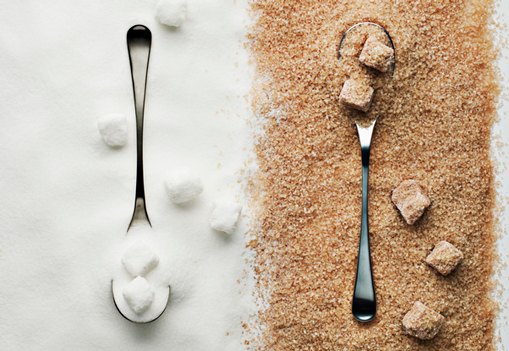
Final Thought

Chemical defoamers provide substantial advantages throughout various industries by successfully managing and lowering foam development. By minimizing foam, chemical defoamers help keep optimal manufacturing prices and decrease downtime connected with foam administration. Chemical defoamers play a crucial duty in mitigating these concerns by quickly breaking down foam, permitting for smoother operations and improved item consistency.
Efficient foam monitoring is similarly vital in wastewater treatment procedures, where too much foam can hinder operations and complicate the treatment of effluents.Foam control is vital in pharmaceutical manufacturing, where the presence of extreme foam can interfere with producing procedures and concession item quality.